Application Summary
The key information we wanted to gain from the test site was how a Powerscreen Chieftain 2200 compared to a Powerscreen Chieftain 2100X (which the customer already owned). In the customers original setup they were using their Chieftain 2100X to screen out a 14mm product, a 10mm product, a 6mm product and a waste dust product. To create these products within the required specification they often needed secondary screening. The Powerscreen Chieftain 2200 was brought into site and setup to the customers preference for testing. At this site in Ballynahinch, a Powerscreen Chieftain 2200 screened ‘Greywacke’ rock.
• Chieftain 2200 increased the efficiency of the screen producing better quality aggregates than the Chieftain 2100X
• Improved fines removal using Chieftain 2200
Setup
A Jaw – set at 125mm CSS
1300 Maxtrak – set at 30mm CSS
1000 Maxtrak – set at 18mm CSS
Chieftain 2200
Chieftain 2100X
A Jaw was being used to Primary crush the material at 125mm CSS. This jaw was feeding a 1300 Maxtrak Cone set at 30mm CSS, feeding a screen with a re-circulation of material entering a 1000 Maxtrak at 18mm CSS.
Chieftain 2100X
Top Deck: 14mm
Middle Deck: 9mm
Bottom Deck: 5mm
Chieftain 2200
Taking 300 tonnes per hour from a 1300 Maxtrak and 110 tonnes per hour of recirculated material from a 1000 Maxtrak
Producing 410 tonnes per hour in total
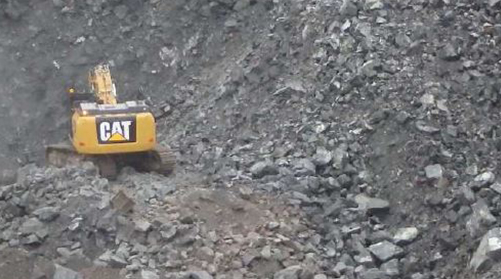
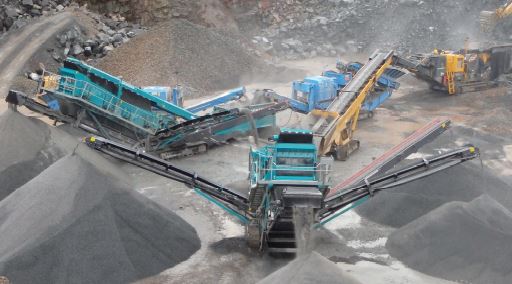
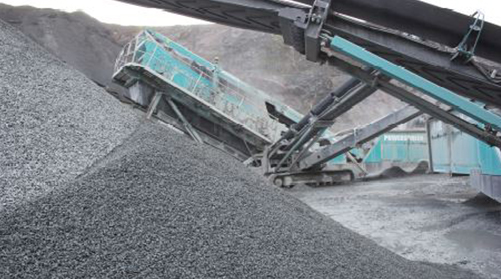
14mm product
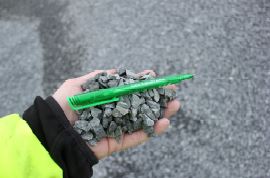
10mm product
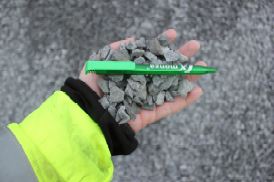
6mm product
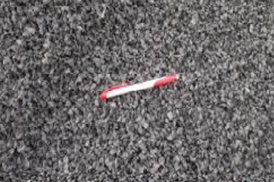
Dust and waste product
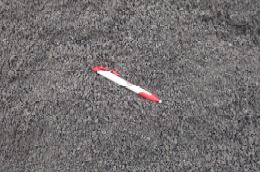